The 14520610 sprocket is a crucial component used in various types of heavy machinery, particularly in tracked vehicles. This guide provides comprehensive information about its features, benefits, applications, installation, and maintenance practices.
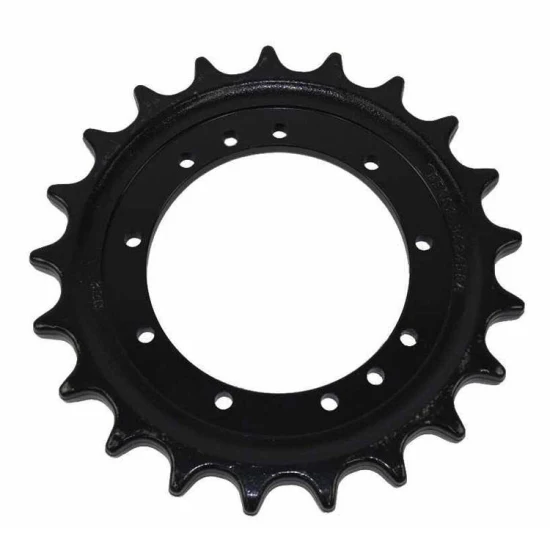
1. Key Features of the 14520610 Sprocket
Specifications
- Material: Typically made from high-strength steel or alloy to ensure durability and performance under heavy loads.
- Tooth Design: Engineered teeth for optimal engagement with tracks, ensuring efficient power transfer.
- Compatibility: Designed to fit specific models of excavators, bulldozers, and other tracked equipment.
Dimensions
- Diameter: Exact measurements vary; it is essential to confirm the diameter based on specific machinery requirements.
- Number of Teeth: Configured with a particular number of teeth to meet operational needs.
2. Benefits of Using the 14520610 Sprocket
- Improved Performance: Facilitates smoother operation and enhances the efficiency of machinery.
- Durability: Built to withstand harsh conditions and heavy loads, resulting in fewer replacements.
- Cost-Effectiveness: Reduces long-term costs due to lower maintenance requirements and extended lifespan.
- Enhanced Traction: Provides reliable track engagement, improving stability and control during operation.
3. Applications of the 14520610 Sprocket
The 14520610 sprocket is commonly found in:
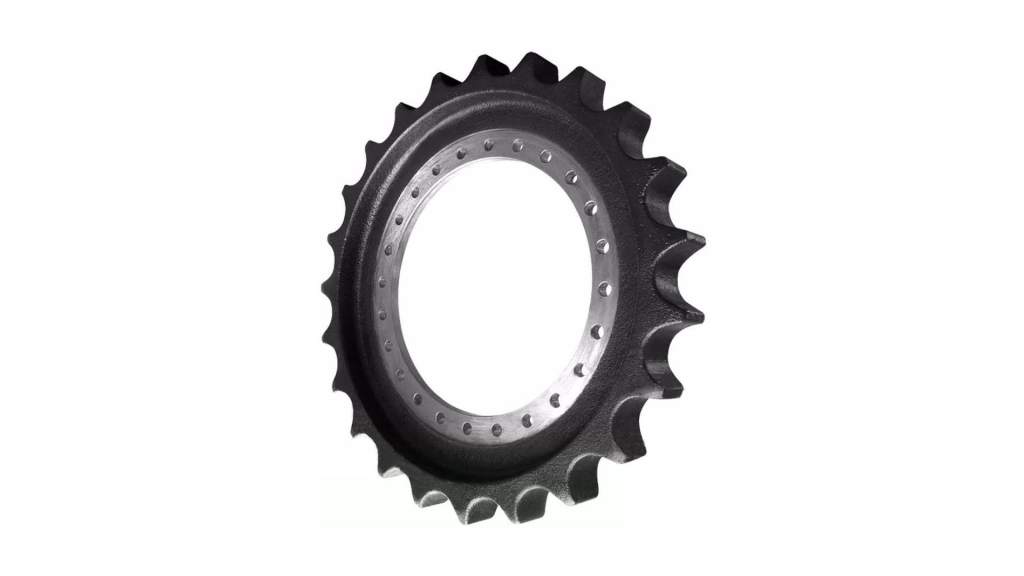
- Excavators: For digging and moving materials effectively.
- Bulldozers: Enhancing pushing and grading capabilities.
- Other Heavy Machinery: Any tracked equipment requiring dependable power transmission.
4. Installation Process
Tools Required
- Wrenches
- Torque wrench
- Lifting equipment (if necessary)
Installation Steps
- Remove the Old Sprocket: Use appropriate tools to detach the existing sprocket.
- Clean the Mounting Area: Ensure the area is free from dirt and debris for a secure fit.
- Position the New Sprocket: Align the 14520610 sprocket with the mounting holes.
- Secure the Sprocket: Attach it using bolts and fasteners, tightening to manufacturer specifications.
- Check Alignment: Ensure proper alignment with the track for optimal performance.
5. Maintenance Guidelines
Routine Inspections
- Visual Checks: Regularly inspect for signs of wear, damage, or misalignment.
- Lubrication: Follow the manufacturer’s recommendations for lubrication intervals to maintain smooth operation.
Cleaning Procedures
- Debris Removal: Keep the sprocket clean from mud and dirt to prevent wear.
- Washing: Use mild detergents and a brush for thorough cleaning when necessary.
Adjustments
- Track Tension: Regularly check and adjust track tension to minimize strain on the sprocket.
6. Troubleshooting Common Issues
Common Symptoms and Solutions
- Uneven Wear:
- Cause: May result from improper installation or misalignment.
- Solution: Reassess the installation and make necessary adjustments.
- Excessive Noise:
- Cause: Could indicate insufficient lubrication or damaged sprocket teeth.
- Solution: Lubricate as needed and inspect for any damage.
- Frequent Failures:
- Cause: Likely due to poor maintenance or incorrect component use.
- Solution: Review maintenance practices and ensure proper part compatibility.
7. Conclusion
The 14520610 sprocket is an essential component that contributes to the performance and reliability of heavy machinery. By understanding its features, benefits, and maintenance practices, you can significantly enhance the effectiveness of your equipment. If you have any further questions or need additional assistance, feel free to reach out!
How to Install a 14520610 Sprocket
Installing the 14520610 sprocket correctly is crucial for the effective operation of your machinery. Here’s a step-by-step guide to help you through the installation process.
Tools and Materials Needed
- Basic Tools:
- Socket set
- Wrenches
- Torque wrench
- Screwdrivers
- Safety Gear:
- Gloves
- Safety goggles
- Replacement Parts:
- 14520610 sprocket
- Any necessary gaskets or seals
Installation Steps
1. Safety Preparations
- Turn Off the Equipment: Ensure the machinery is powered down and parked on a stable surface.
- Use Wheel Chocks: Secure the equipment with wheel chocks to prevent any movement during installation.
2. Remove the Old Sprocket
- Access the Sprocket: Depending on your machinery, you may need to remove covers or guards to access the sprocket.
- Loosen Fasteners: Use the appropriate socket or wrench to loosen and remove the bolts securing the old sprocket.
- Remove the Old Sprocket: Carefully pull the old sprocket off the shaft. If it’s stuck, gently tap it with a rubber mallet to free it.
3. Prepare the New Sprocket
- Inspect the New Sprocket: Check the 14520610 sprocket for any damage or defects before installation.
- Clean the Shaft: Wipe down the shaft where the sprocket will be mounted to ensure a clean fit.
4. Install the New Sprocket
- Position the Sprocket: Align the new sprocket with the shaft, ensuring that any keyways or alignment marks are properly matched.
- Secure the Sprocket: Slide the sprocket onto the shaft until it is fully seated.
5. Fasten the Sprocket
- Install Bolts: Insert and hand-tighten the bolts that secure the sprocket to the shaft.
- Torque Specifications: Use a torque wrench to tighten the bolts to the manufacturer’s specified torque settings. This ensures a secure fit without over-torquing.
6. Reassemble Any Removed Components
- Replace Covers or Guards: If you removed any components to access the sprocket, reattach them securely.
- Double-Check Fasteners: Make sure all fasteners are tightened appropriately.
7. Final Checks
- Inspect Installation: Look over the installation to ensure everything is aligned and secured correctly.
- Run a Test: Start the machinery and run it at low speed to check that the sprocket operates smoothly without unusual noises or vibrations.
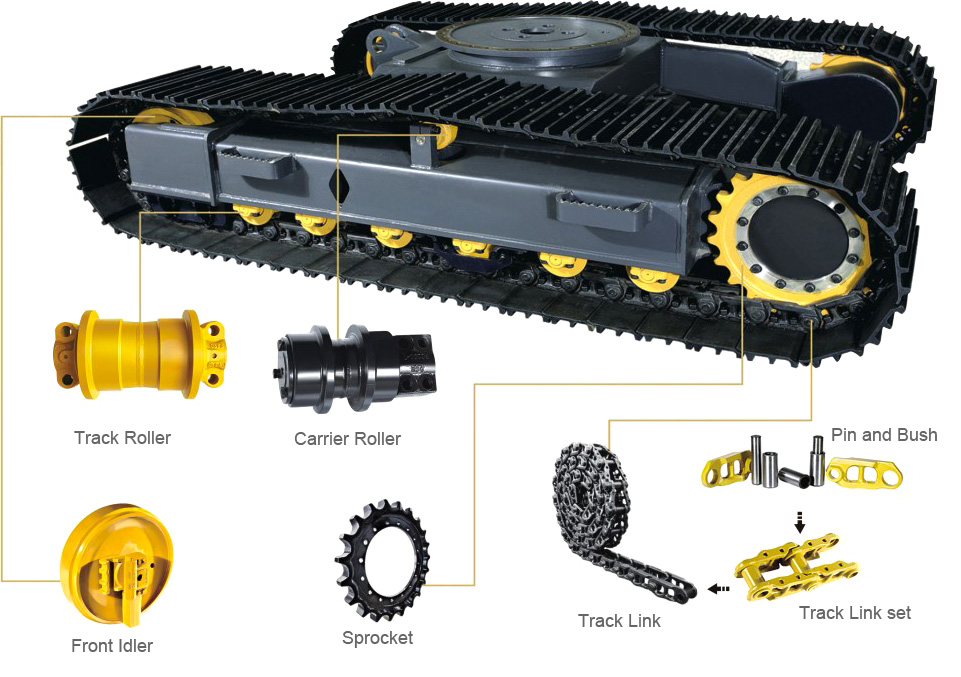
Undercarriage parts
The excavator undercarriage is the foundation that supports the entire machine, consisting of critical components such as track shoes, rollers, idlers, and sprockets that work together to provide traction, stability, and mobility. These durable parts are engineered to withstand the intense stresses and harsh operating conditions encountered during construction, demolition, and earthmoving tasks, and their proper maintenance and replacement are crucial for ensuring the excavator’s long-term performance and reliability. The undercarriage plays a vital role in the excavator’s overall capabilities, enabling it to traverse a wide range of terrains and job site conditions with confidence and efficiency.